DMG Spindle Repair
When it comes to CNC machines, the spindle is a critical component that plays a vital role in the overall performance and precision of the machine. One of the popular spindles used in DMG CNC machines is the Kessler spindle, known for its high-quality craftsmanship and reliability. However, like any mechanical component, the Kessler spindle is susceptible to wear and tear over time, requiring maintenance and repair to ensure optimal functioning.
Why Repair Spindles in a Clean Room Environment?
Repairing a Kessler spindle from a DMG CNC machine in a clean room environment is crucial for several reasons:
- Prevention of Contamination:
The precision components of the spindle are highly sensitive to contamination. Dust, dirt, or debris can significantly impact the performance and lifespan of the spindle. Repairing the spindle in a clean room environment helps minimize the risk of contamination and ensures that the spindle operates at its peak efficiency. - Maintaining Precision:
The Kessler spindle operates at high speeds and tolerances, requiring utmost precision during repair. A clean room environment provides the necessary conditions for technicians to work with precision tools and equipment without the risk of external factors affecting the repair process. - Enhanced Durability:
By conducting the repair in a clean room environment, the likelihood of introducing foreign particles that could compromise the spindle’s durability is greatly reduced. This ensures that the repaired spindle will continue to function optimally for an extended period.
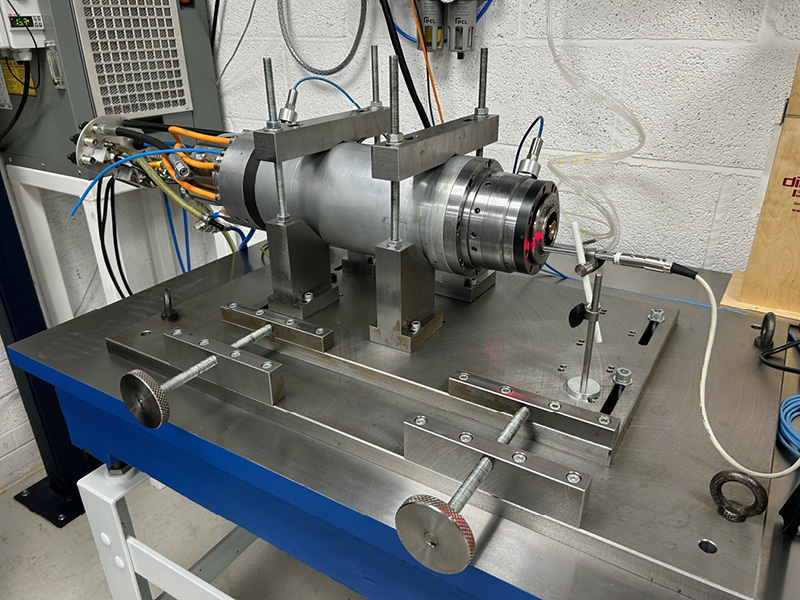
Functional Testing on Test Rigs
Once the repair of the Kessler spindle is completed in a clean room environment, the next crucial step is to conduct thorough functional testing on test rigs. Test rigs are specialized equipment designed to simulate the operating conditions of the spindle and evaluate its performance post-repair. This step is essential to validate that the spindle is functioning as intended and meets the manufacturer’s specifications.
Validation Report for the Customer
To provide assurance to the customer that the repaired Kessler spindle is in optimal working condition, a validation report is prepared. This report details the testing procedures conducted, the results obtained, and confirms that the spindle has been restored to its original functionality. The validation report serves as a quality assurance document that gives the customer confidence in the repair work performed on their CNC machine.
In conclusion, repairing a Kessler spindle from a DMG CNC machine in a clean room environment, followed by functional testing on test rigs and providing a validation report, ensures that the spindle is restored to its peak performance. This meticulous approach not only prolongs the lifespan of the spindle but also enhances the overall efficiency and accuracy of the CNC machine.
For more information regards our repairs of DMG CNC spindles, please contact CNC Repair (UK) Ltd on 0800 043 1800.
Contact
Tel:
0800 043 1800
Email:
support@cncrepair.co.uk
CNC Repair (UK) Limited
Unit 4 Spalding Road Business Park,
Bourne,
Lincolnshire PE10 9LF
Navigate
HSD Spindle Repair
When it comes to precision machining and high-speed cutting operations, many manufacturers choose...
Haas spindle repair and rebuild
American machine tool builder Haas build a wide range of quality machine tools. Due to their...